Scientists Report on Carbon Footprint Reduction of Low-emissions Cement and Carbonated Concrete During International Congress on the Chemistry of Cement
Researchers from Solidia Technologies®, LafargeHolcim (France), and the U.S. Federal Highway Administration (FHWA) presented results of tests on a new cement that lowers carbon emissions during production and gains strength through carbonation during the 15th International Congress on the Chemistry of Cement (ICCC).
This press release features multimedia. View the full release here: https://www.businesswire.com/news/home/20191010005636/en/
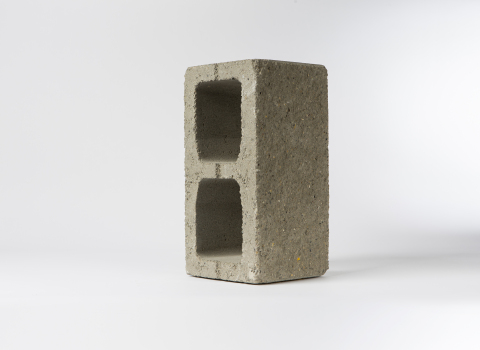
Made with low-emissions, low-energy Solidia Cement™ and cured with CO2, Solidia Concrete™ reduces the carbon footprint of concrete up to 70% over traditional concrete. (Photo: Business Wire)
Made from raw materials that are typically used to make ordinary Portland cement (OPC) clinker, the new cement is based on calcium silicates. The researchers reported a 30% reduction in energy use and up to a 30% reduction of CO2 emissions during production compared to conventional cement. The tests also revealed that, during the carbonation process, it can sequester up to 300 kg of CO2 per ton of cement, resulting in an up to 70% reduction in the overall carbon footprint compared to traditional concrete. Tests of concrete strength, elasticity, durability such as resistance to freezing and thawing, sulfate resistance, and alkali silica reaction (ASR) met all industry standards.
Research Engineer Vincent Meyer of LafargeHolcim (France) and Solidia researchers Jason Bryant and Sada Sahu, Ph.D., presented “Calcium Silicate Cement and Mineral Carbonation Applied to Precast Industry.” As part of their test protocol, five different clinkers were produced in a pilot rotary kiln with raw materials coming from industrial quarries. Various raw materials were used to create the five raw mixes with different raw mix chemistries to assess the robustness in clinkerization process. Thermodynamic simulations were carried out to understand the burning behavior and phase composition at various temperatures. The simulated results were compared to kiln behavior and clinker quality. Finally, five different cements were tested at lab scale and some pavers were produced to assess the cements quality towards carbonation.
In summary, they reported that: “Calcium silicate cement containing non-hydraulic phases is produced in existing cement kilns using the same raw material as Portland cement. The key difference is that this type of cement is produced using less limestone and at lower kiln burning temperatures. This translates to reduced CO2 emissions during cement manufacturing (30% reduction). The concrete production process involves mixing cement, aggregates, sand, and water that is reacted with CO2 to form a durable matrix. The curing process can capture up to 300 kg of CO2 per ton of cement used. Together, the calcium silicate cement and concrete production reduce the CO2 footprint by 70% when compared to conventional cement and concrete products.”
A second presentation by Dr. Sahu and FHWA Research Civil Engineer (Highway) R.C. Meininger, “Performance of CO2-Reducing Cement Based on Calcium Silicates,” revealed similar sustainability benefits. Concrete made using this new cement was tested using ASTM C39 (compressive strength), C78 (flexure strength), C469 (splitting tensile strength), and C496 (modulus of elasticity); durability performance following ASTM C666 (freezing and thawing resistance), C227 (ASR); and C1012 (sulfate resistance). It exhibited mechanical properties equivalent or better than OPC-based concrete and had negligible mass loss due to scaling during the freeze-thaw testing. It passed ASTM C666 in fresh water while maintaining a relative dynamic modulus of elasticity >90% after 540 freeze-thaw cycles. Similarly, mortar bars made with the new cement exhibited excellent resistance to sulfate attack and excellent resistance to ASR.
The joint research conducted with LafargeHolcim was sponsored by the Solid Life project, which is granted by the EU under the LIFE program. The latter research was conducted at the FHWA-Turner Fairbanks Highway Research Center under a cooperative agreement between Solidia Technologies and FHWA for evaluating technologies with respect to potential applications in highway construction and repair. The cement is produced by LafargeHolcim and is now commercially available as Solidia Cement™ and the resulting concrete products as Solidia Concrete™.
About Solidia Technologies®
Based in Piscataway, N.J. (USA), Solidia Technologies® is a cement and concrete technology company that makes it easy and profitable to use CO2 to create superior and sustainable building and construction materials. Solidia’s investors include Kleiner Perkins, Bright Capital, BASF, BP, LafargeHolcim, Total Energy Ventures, Oil and Gas Climate Initiative (OGCI) Climate Investments, Air Liquide, Bill Joy and other private investors. Follow Solidia at www.solidiatech.com and on LinkedIn, YouTube and Twitter: @SolidiaCO2.
View source version on businesswire.com: https://www.businesswire.com/news/home/20191010005636/en/