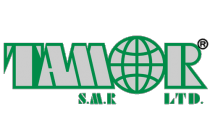
Categories
- Composites, Plastics & Rubber
- Mechanical, Electro-mechanical, Hydraulic and Pneumatic components
- Metal Processing, Parts & Components
- Military, Tactical, Logistic Support Vehicles & related equipment
Tamor S.M.R Ltd., specializes in the production of Metalwork and Rubber Vulcanized Kits, Assemblies and Components for heavy vehicle applications for Defense and Industry. The company’s manufacturing floor supports rubber vulcanization by bonding rubber to metal or rubber molding. Metal fabricating technologies include cold deep drawing, forming, cutting, bending, welding, 5-Axis CNC machining and milling, painting and preservation – all under one roof - all per customers’ specifications and requirements.
HISTORY
Tamor S.M.R Ltd was founded on June 15, 1988. It started as a producer of rubber bonded to metal and rubber parts for heavy vehicles; primarily for military applications. Tamor mainly manufactured track shoe assemblies and components and solid rubber wheels.
In 1996, Tamor S.M.R expanded its product line to supply the heavy vehicle and industrial sectors with manufactured metal products. The company expanded its line to products such as fuel tanks, water storage tanks, electric battery case covers, made of armored aluminum for on-board of the Merkava tank, as well as a new range of steel and non-ferrous metal items. To enable less dependency on subcontractors, Tamor developed its capacities to include the production of the steel and aluminum wheels required for its solid rubber wheels and track steel components.
Today, the maturity of Tamor’s manufacturing capabilities, its knowledge and experience in fabricating metal and rubber and the implementation of adapted technologies have resulted in the company’s ability to produce logistically complicated kits, subassemblies and innovative products for Defense and Industrial applications worldwide.
QUALITY
At Tamor, implementing and maintaining rigorous Quality Control and Quality Assurance standards are core factors for developing, manufacturing and delivering reliable, top grade products.
Tamor S.M.R Ltd., ISO 9001:2008 certified, has been long qualified as a designer and manufacturer of rubber, rubber bonded to metal and metal components and assemblies for tracked and wheeled vehicles.
As a Defense contractor, Tamor has received AQAP-2110 approval, as required by NATO, to serve European customers. The U.S.A. Tank-Automotive and Armaments Command (TACOM) has long recognized Tamor as a Qualified Supplier placing us on the QSL 01, QSL 03 and QSL 04 TACOM lists. The QSLs (Qualified Supplier Lists) include major assemblies’ suppliers and full combat vehicles suppliers to the U.S. Government.
Tamor’s military products have been field tested and qualified by the Israeli Defense Forces.
Wheels
ROAD WHEELS
SUPPORT WHEELS
TENSION WHEELS
IDLER WHEELS
Worldwide, Armies use Tamor's field-tested solid rubber wheels and metal wheels on Main Battle Tanks, Infantry Fighting Vehicles, Armed Personnel Carriers, Amphibious Tracked Fighting Vehicles, Military Trucks and other heavy military vehicles.
The various in-house technologies supported at Tamor are implemented to produce, among others, solid rubber wheels and metal wheels for military vehicles such as the M1, M-2, M9, M48, M-60, M-88, M-109, M-113, LVTP 7, AMX-113, LEOPARD 1, LEOPARD 2, MERKAVA (all Marks) and others.
Track Assemblies
Track shoe assemblies, track shoes and track pads are supplied for military vehicles such as Main Battle Tanks, Armored Personnel Carriers, Armored Recovery Vehicles and other heavy Tanks including the M-1, M-2, M-60, M-88, M-109, M-113, AMX-113, Leopard I and II and others.
TRACK SHOE ASSEMBLIES
Tamor SMR Ltd track shoe assemblies are supplied as single track shoes, in sections of eight (8) linked track shoes or as complete, fully rolled track assemblies for the left and right sides of military tanks.
TRACK SHOES AND TRACK PADS
Depending on the model, track shoes are supplied with either detachable or permanent rubber track pads. Machining and vulcanization takes place in-house at the Tamor factory as track shoe bodies, track pads and bushings, pins and connectors are prepared to turn individual track shoes into sections or rolled track assemblies.
Fuel Tanks
Fuel Tanks offered by the Tamor S.M.R. factory have been designed, developed and manufactured for various military vehicles including the Merkava (Mark) battle tanks, Puma tracked infantry fighting vehicle (IFV), armoured personnel carriers (APCs) and Oshkosh military trucks.
Dynamic fuel tanks and Static fuel tanks (for power generators, heating systems) are manufactured from various materials including:
*Steel * Stainless Steel * Aluminum * Armored Aluminum
Fuel tank assemblies are supplied with fuel tanks, pumps, hoses, tubes, fuel gauges, brackets, shock absorbers and other accessories.
The Research and Development stages of fuel tanks involve 3D designs, mock-ups, samples and pilot production to final serial production. The results are fuel tanks with symmetric and asymmetric designs that offer optimal use of space under the hood.
In-house, Tamor’s facility offers testing equipment to conduct:
Leakage testing under inner pressure
Vibration testing simulations under extreme road conditions
Tamor is certified for welding according to American AWS D 1.1 and AWS D 17.1 and European DIN standards.
Chassis and Suspension
Tamor manufactures all arms - suspension arms, idler arms and all other position arms for tracked vehicles. They can be delivered assembled with the wheels.
We also manufacture control arms, cross members and frames, chassis and suspension assemblies for heavy military trucks and other wheeled military vehicles.
Utilizing in-house technologies and manufacturing capabilities, Tamor designs and manufactures its own tooling and jigs, supplying the individual components and assemblies for the chassis and suspension systems per Customers' specifications.
Antivibration - Rubber
Tamor's custom made rubber antivibration products have been used in specific military applications to reduce the negative impact of noise, shocks and vibrations.
Special rubber compounds are developed and manufactured to meet customers’ custom requirements.
Rubber Shock Absorbing Pads
In Armed Forces applications, thick rubber shock absorbing pads have been used on the inner frames of huge steel containers used to store and transport heavy tank engines and transmissions.
Antivibration Rubber Mats
In Naval applications, Tamor's thin antivibration rubber mats have been used to safeguard sensitive instruments from idling frequency of engine vibrations.
Metalwork
LARGE METALWORK STRUCTURES
These large, metal, storage and transportation containers, built to customer (TACOM – USA Army) design and per military specification, required the implementation of Tamor’s in-house rubber vulcanization and metalwork processes and technologies.
Cutting, bending, CNC milling and machining (horizontal, vertical and turning), welding, shot blasting (shot peening), painting and preservation are used to build massive structures per customer specifications and drawings.
Water Tanks
WATER TANKS - FOR DRINKING WATER
These asymmetrical, drinking water tanks manufactured by Tamor SMR are made from steel, stainless steel or aluminum sheets that are cut, bent, formed and welded (TIG, MIG) in-house to attain their shapes and dimensions. The vessels are treated for corrosion resistance and painted.
Tamor's approach to meeting special customer requirements result in our ability to manufacture unique, irregular shaped water tanks to optimize the use of assigned space and to maximize the actual volume of the water tanks.
Testing of the final products includes testing for leaks under inner pressure and vibration simulations under extreme road conditions.
Other Products
EXERCISE AMMUNITION
Exercise ammunition developed by Tamor can be used repeatedly due to its flexible surface. They are built according to original size, shape, weight and center of gravity as the original product.
PORTABLE SIGNPOSTS - RUBBER VULCANIZED
Tamor manufactures portable, foldable signposts used by the military to cordon off dangerous areas. Several signposts can be linked together. The sturdy base is made of steel and vulcanized rubber.
Built to customer specification, Tamor implements in-house technologies and manufacturing capabilities including rubber vulcanization to produce these flexible, rubber covered, metal based signposts.
5-Axis CNC Machining Center
During 2013, Tamor SMR acquisition of unique CNC equipment enabled diversification of the product line within their manufacturing facility.
Results were:
• Successful machining of large high precision items
• Specialization in machining a variety of castings and metals
Integration of 2 large CNC 5-Axis machines resulted in the successful machining of large, high precision items including:
• M1 Hatches
• Mechanical Housings
• Idlers
• Other products
Utilizing 5-Axis CNC machining, Tamor developed its specializations in machining of:
• Armor Steel Castings
• Armor Steels
• Other types of castings
• Other popular metals such as aluminum
Advantages
• Production of complex items
• Elimination of multiple set ups
• Efficient machining of angular surfaces
• RMT - Reduced Machining Time
• Better Surface Finish
• Elimination / Reduction of Manual Millwork and Handwork
• Elimination of Extra Tooling and Fixtures
Rubber Vulcanization
At Tamor SMR Ltd, manufacturing of Rubber Bonded to Metal and Rubber Molded items is achieved through the processes of:
- Injection Molding
- Transfer Molding
- Compression Molding
Tamor SMR takes the rubber, implements the various molding methods on its production floor and produces high quality, durable and reliable end products for industrial applications in Defense, Transportation and other Commercial sectors.
Injection Molding involves preheating the rubber compound while it's being processed through an extruder. Using high pressure, the compound is injected into the mold cavity for a certain time, pressure and temperature. Typical items include high quantity small products weighing between a few grams to several kilograms. Cycle time is relatively short and the injection presses and the molds are relatively expensive.
Transfer Molding is a technique that combines injection and compression molding technologies. Transfer molding requires building a "piston and cylinder"-like device in the mold and squirting the rubber into it through small holes. When the mold is closed and under hydraulic pressure, the rubber is forced through the small hole into the cavity where it cures. Transfer molding is usually used for heavier rubber parts or in places where it is desirous to shorten the cycle time and produce rubber with uniform properties. Transfer molds are more expensive than the ones used in compression molding.
Compression Molding is the classic rubber vulcanization method. A defined excess amount of the bulk rubber compound is placed in the cavity of the mold. Using increased pressure and temperature, the rubber compound is formed. It is the excess material in the cavity that provides the required pressure. Molds are relatively simple and help in studying shrinkage of rubber and producing first samples of various rubber compounds. This method is generally the most suitable method for low and medium sized serial production.
Deep Drawing Process
At Tamor, the manufacturing of wheels can require the application of up to 1400 tons of pressure as flat, shiny metal discs are inserted into the tool dies and a hydraulic press forms the steel to its appropriate thickness and depth - this can mean a deep drawn item of up to a thickness of 12.7mm and a depth of 170mm.
Deep drawing is a metal forming process that provides many challenges. The result must be a metal shape without cracks, wrinkles or breakage. As the manufacturer, we thoroughly evaluate the type of metal used, its thickness, the tool surface finish, the type of lubricant used, the size and shape of the blank (the flat metal part that will be deep drawn), the punching speed, draw radii, draw ratio, draw bead height and shape.
Welding Process
Depending on the application and the product being manufactured, Tamor factory welders are qualified for MIG welding, also known as Gas Metal Arc Welding and TIG welding, also known as Gas Tungsten Arc Welding.
TIG Welding is used to produce high quality precision welds offering low distortion and precise control of welding variables such as heat.
MIG Welding is considered to be a semiautomatic process. Long welds can be made without starts and stops. Primary shielding gases used are Argon and CO2 .
Tamor's welding stations offer flexibility and were built with the comfort of the welder in mind. As a product is being welded, the welder can turn and adjust the angles of the item enabling him better control throughout the welding process.
Throughout the manufacturing process, Tamor's Quality Assurance team ensures that testing parameters are met and upheld in accordance with the requirements of, among others:
- Magnetic particle testing
- Liquid penetrant testing
- Non destructive testing
- Leakage testing
- Drop fall testing
- Vibration testing
Factory welders are trained to work and qualified in accordance with European DIN standards as well as American AWS standards. Examples of Tamor's welding certifications include AWS D 1.1, AWS D 17.1 and DIN 6700 EN 15085-2 Class I (used particularly for the railroad industry).
Painting & Preservation Process
Depending on the requirements of a manufactured item, metal surfaces undergo several painting and preservation stages within the Tamor factory before emerging as corrosion free, finished end products.
In-house, Tamor offers:
- Shot peening or sandblasting to remove rust and produce smooth surfaces
- Chemical coating
- Degreasing and rinsing
- Painting with rust inhibiting primers
- Painting with water based or solvent based paints
- Adhesive Spraying Station
- Wet spray painting
- Electrostatic spray painting
Tamor SMR Ltd.
- Southern Industrial Zone – P.O.B. 19 Hacharoshet 6 Street, 23100, Migdal Haemek, Israel
- +972 (4) 654 6735
- +972 (4) 654 6738
- main@tamor.co.il
- www.tamor.co.il