ExOne Announces New 3D Printing Materials, Bringing Total to 21 Metals, Ceramics and Composites
The ExOne Company (Nasdaq: XONE), the global leader in industrial sand and metal 3D printers using binder jetting technology, today announced that 15 new metal, ceramic and composite materials have been qualified by ExOne and its customers for 3D printing on the company’s family of metal 3D printers.
This press release features multimedia. View the full release here: https://www.businesswire.com/news/home/20200225005229/en/
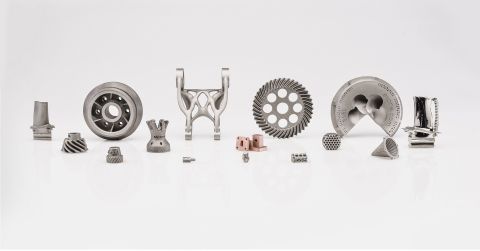
Metal 3D printers from The ExOne Company now binder jet 21 total materials, including 10 single-alloy metals, six ceramics, and five composite materials. Additionally, more than 24 materials are approved for controlled R&D printing. This photo showcases a variety of ExOne’s qualified and R&D materials, including M2 Tool Steel, 316L, 304L, 17-74PH, copper, and Inconel 625. (Photo: Business Wire)
With these additions, owners of ExOne metal 3D printers can now print 21 qualified materials: 10 single-alloy metals, six ceramics, and five composite materials. More than 24 additional powders have been qualified for 3D printing in controlled research and development environments, including aluminum and Inconel 718.
ExOne’s exclusive binder jetting technology, in development since 1996, transforms powdered materials into dense and functional precision parts at high speeds. Binder jetting is a method of 3D printing in which an industrial printhead deposits a liquid binder onto a thin layer of powdered particles, layer by layer, until the object is formed.
“ExOne continues to make aggressive and outstanding progress in qualifying new materials for 3D printing on our machines,” said ExOne CEO John Hartner. “Qualifying a new material for binder jet 3D printing is complex work that involves optimizing how materials, machines and processes work together. We would like to thank our customers and partners for their assistance in accelerating this important work, which is enabling more sustainable manufacturing and part designs.”
Partners that have assisted ExOne in qualifying materials include Global Tungsten & Powders, H.C. Starck Solutions, NASA, Oak Ridge National Laboratory, SGL Carbon, the U.S. Army, the U.S. Department of Energy, the University of Texas at El Paso, and Virginia Tech. In all, ExOne customers are now 3D printing more than a dozen different materials for R&D, prototypes, and production, including proprietary materials.
Binder jet 3D printing is a sustainable method of metal part production because it fabricates objects with little to no waste and, at the same time, enables all-new lightweight designs that were not previously manufacturable.
What’s more, binder jetting can produce parts at high speeds and volumes that can enable widespread use of this sustainable technology.
Fast-Tracking Aluminum
ExOne believes the ability to 3D print some materials at high speeds, such as aluminum, will have a transformative, sustainable effect on the automobile and aerospace industry.
“While our teams can binder jet aluminum in controlled R&D environments today, we believe that optimizing this material for high-speed 3D printing will eventually transform how car and airplane parts are made, making them smarter and lighter weight,” said Rick Lucas, Chief Technology Officer at ExOne. “Based on high demand from the marketplace, we have fast-tracked development of this material for use on our machines.”
To accelerate this work, ExOne is also collaborating with a number of manufacturing companies to optimize commercial 3D printing of aluminum.
New Qualification System
Starting today, ExOne has three material qualification levels that recognize different degrees of material readiness for customers with different application needs.
Third-Party Qualified Materials | |
These seven materials have passed rigorous ExOne tests over multiple builds and have verified material property data from an independent third party. |
|
|
Customer-Qualified Materials | |
These fourteen materials have been qualified by ExOne customers with their own standards and are being successfully printed today for their own applications. |
|
|
R&D Qualified Materials |
|
These 26 materials have passed a preliminary qualification phase by ExOne and are deemed printable, supported by ongoing development. |
|
|
ExOne’s family of metal 3D printers includes the Innovent+, an entry-level system used globally for R&D, design and small part production; the X1 25Pro, a mid-sized production 3D printer that is large enough for most metal parts manufactured today; and the X1 160Pro, the company’s largest metal 3D printer that is slated for delivery later this year.
About ExOne
ExOne is the pioneer and global leader in binder jet 3D printing technology. Since 1995, we’ve been on a mission to deliver powerful 3D printers that solve the toughest problems and enable world-changing innovations. Our 3D printing systems quickly transform powder materials — including metals, ceramics, composites and sand — into precision parts, metalcasting molds and cores, and innovative tooling solutions. Industrial customers use our technology to save time and money, reduce waste, improve their manufacturing flexibility, and deliver designs and products that were once impossible. As home to the world’s leading team of binder jetting experts, ExOne also provides specialized 3D printing services, including on-demand production of mission-critical parts, as well as engineering and design consulting. Learn more about ExOne at www.exone.com or on Twitter at @ExOneCo.
View source version on businesswire.com: https://www.businesswire.com/news/home/20200225005229/en/